DEPARTMENTS
ROLAND C. JONES, CIH, LEED GA,
is a senior project manager with Environmental Connection, Inc. in
New York City. He can be reached at RJones@VTIHQ.com.
Editor’s note: References to specific products or services in this article do not consitute endorsement by AIHA or The Synergist.
As an industrial hygienist, much of my practice has focused on indoor air quality and environmental issues in commercial buildings. Early on, I understood that “sustainable” design and construction methods, including those referenced in the Leadership in Energy and Environmental Design (LEED) rating system, aligned with the best practices that our firm recommends for improved indoor environmental quality.
In 2010, I encountered the International Living Future Institute’s (ILFI) Living Building Challenge (LBC), and was intrigued by its simple yet stringent approach. Shortly after I became an ILFI Ambassador, an LBC Collaborative was forming in New York City to facilitate Living Building projects. At the first meeting, in the summer of 2011, we were five strong. Today, the Collaborative consists of more than thirty architects, engineers, sustainability consultants, construction managers, developers, and industrial hygienists.
Our Collaborative has investigated and analyzed hurdles (regulatory and otherwise) to widespread adoption of the LBC in metropolitan New York. The hurdles are not surprising, given the unconventional nature of the LBC. Barriers related to feasibility, scale, perception, cost, and logistics are also being vetted by our Collaborative research team.
BARRIERS TO ADOPTION
The LBC “petals,” or performance areas, most relevant to industrial hygienists are the “health and happiness petal” and the “materials petal.” We identified no significant regulatory barriers for the health and happiness petal, which requires operable windows in regularly occupied spaces, best practices for indoor air quality, and aspects of biophilia in the design. However, technical and logistical barriers were identified in areas such as energy code requirements for high-rise construction, given the predominance of glass-curtain wall designs and the relative absence of occupant control.
No specific regulatory barriers were found for the materials petal, which prohibits use of more than 20 ILFI “Red List” chemicals, and requires purchase of carbon offsets, use of sustainably grown or extracted materials, regional products, and waste reduction. The most prevalent barriers the team found were procedural—for example, the significant time commitment necessary to identify compliant building materials, and the difficulty obtaining sufficient chemical information from product manufacturers. It is notable that LBC is part of a larger movement toward material transparency (see earlier Green Building columns in The Synergist), which signals opportunities for industrial hygienists as interpreters of such information.
CASE STUDIES
Discussions with two NYC building owners illustrate some surmountable obstacles to achieving LBC certification. Robert Scarano, an architect and developer, has designed the Bright’N’Green project, a six-unit residential condominium in Brighton Beach, Brooklyn. Scarano is going all out in his quest to be Exhibit A for the new normal of sustainable construction. The project has garnered Green Globes certification, and is working toward LEED Platinum and full LBC certification. Net Zero Energy (NZE) will be achieved through use of renewable energy and conservation measures including a rooftop and window awning solar array and solar hot water tubes; geothermal heating and cooling; an envelope built to Passive House standards; and energy recovery ventilation systems. The project also boasts a regenerative elevator and wind turbines. Air quality will be addressed using an Advantix air purification system employing a liquid desiccant to remove micro-organisms and bacteria and to lower humidity. Scarano is also exploring a specialized filter system designed specifically to capture nanoparticles released from stovetop cookware. Building materials were vetted by Scarano’s team to avoid any products with “Red List” chemicals.
The project team searched for five months to find bathroom vanities with no Red List chemicals, and ended up custom-building the vanities instead. Flooring is primarily salvaged wood installed over plywood sheeting certified by the Forest Stewardship Council (FSC). The project is intended to become one of only five (so far) full LBC-certified projects in the world. The advanced sustainability comes at a price, with soft costs (design, engineering, consulting) exceeding hard costs (labor, materials) according to Scarano’s estimates.
The townhouse project on 130 West 95th Street in Manhattan encountered a different set of difficulties. As detailed on the website of owner and developer Abel Hahn (ViridianFuture.com), one of the biggest challenges in New York City can be the permit process, especially when novel approaches and technologies are included. New York has recently enacted legislation to remedy this issue, with an inter-agency team reviewing innovative processes and technology, but the permit application period can still be arduous.
Hahn was no stranger to sustainable building practices when he and his wife purchased the townhome in February 2013. They had already planned to renovate to LEED Platinum as well as Passive House standards when the couple decided to target full LBC certification. However, obstacles arose, including a regulation limiting roof coverage by photovoltaic panels, so firefighters would have a clear path; and the significant cost of installing geothermal wells through bedrock. Black water processing technology was determined to take up too much space, thwarting “water petal” compliance. The project is on track to obtain the “materials petal” certification by careful vetting of all materials, as well as the salvage and re-use of building materials. Solar panels, an envelope built to Passive House standards, and the use of energy recovery ventilation systems will contribute to near NZE.
Hahn is looking forward to showing the community that sustainable does not mean Spartan. Design features including an open staircase and circular glass elevator are certain to prove his point. Although design and construction costs are high, Hahn indicated that comparables in the neighborhood reflect that the investment is sound not only environmentally and ethically, but financially as well.
Sustainable, but Not Spartan:
Case Studies in Sustainable Building Design
BY ROLAND C. JONES
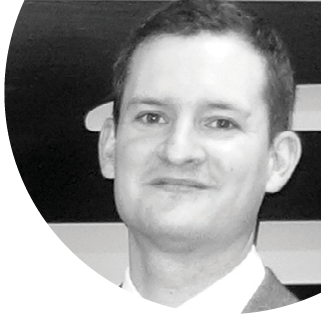
GREEN BUILDING
LINKS:
• Back to Summary Page
Bad Actors on the LBC Red List
LBC tags “worst-in-class” Red List chemicals for exclusion from LBC buildings. Many are bad actors long familiar to industrial hygienists: asbestos, cadmium, chlorinated polyethylene and chlorosulfonated polyethylene, chlorofluorocarbons (CFCs), chloroprene (neoprene), formaldehyde (added), halogenated flame retardants, hydrochlorofluorocarbons (HCFCs), lead (added), mercury, petrochemical fertilizers and pesticides, phthalates, polyvinyl chloride (PVC) and wood treatments containing creosote, arsenic or pentachlorophenol.
The red-listing of chemicals pushes the market forward. This is best done carefully to avoid regrettable substitutes. For information about safe ingredients, visit the Cleangredients database (www.cleangredients.org) and EPA’s Design for Environment Safer Chemical Ingredients List (www.epa.gov/dfe/saferingredients.htm).
— Catherine Bobenhausen, CIH, CSP, LEED AP BD+C, cbobenhausen@vidaris.com.
• The Synergist TOC