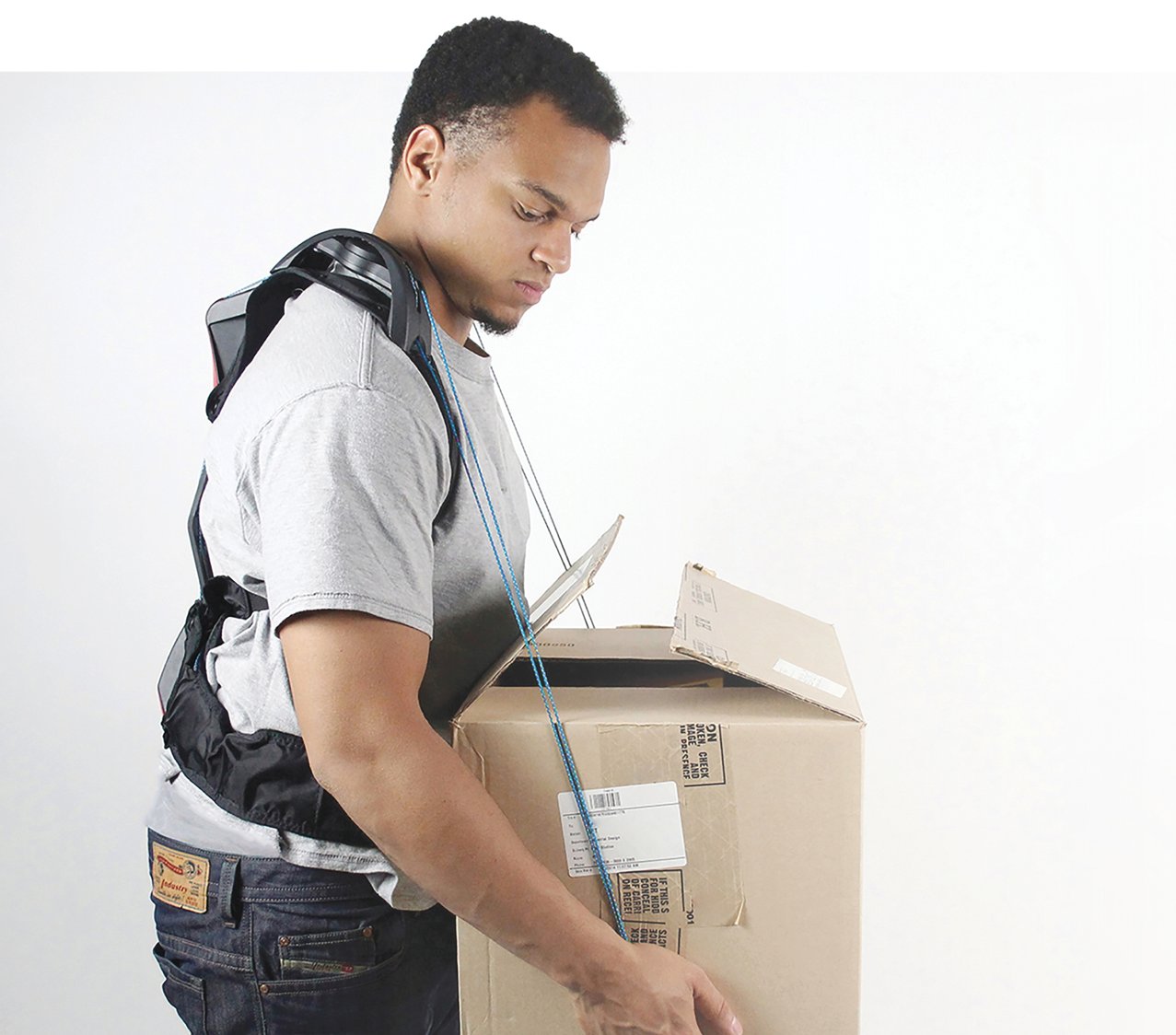

Wearable
Help
The Potential Applications of Human Exoskeletons
BY MICK SNYDER
Editor’s note:
The opinions expressed in this article are the author’s and do not necessarily represent those of AIHA orhotos are used with permission from StrongArm Technologies.
Google Glass, Fitbit, the Apple Watch: wearable technology is the latest craze, and it’s seeping into every aspect of our lives. By one estimate, the total value of the wearables market worldwide is expected to top 19 billion dollars in 2018.
One special type of wearable technology holds particular promise for workplace health and safety, including potential applications in industry, healthcare, the military, and other arenas. Human exoskeletons are external structures or “suits” that support wearers in some fashion. In many ways, exoskeletons provide truly superhuman strength. They can be used to help lift heavy loads; hold a heavy tool over one’s head; walk faster, farther, and with less fatigue while carrying heavy items or rucksacks; and lift patients. They can even help paraplegics walk without crutches or other supports. Workers wearing an exoskeleton can sustain awkward postures, hold heavy tools, and absorb movement and vibration, potentially reducing stressors on the body and, therefore, reducing injuries.
While exoskeletons have been in use for several years, older versions were heavy, bulky, cumbersome, and extremely expensive. Newer technology, materials, and creative thinking is leading to development of wearable “help” that has potential to prevent injuries and increase productivity without being prohibitively expensive or so unwieldy workers don’t want to use them.
Traditional exoskeletons utilize a stiff frame (typically metal or carbon fiber) with a power source; some look like wearable robots. As human exoskeletons become easier to use and more cost effective, they are likely to be used increasingly in healthcare and industrial settings over the next few years.
Some manufacturers, sensitive to the associations of the term “exoskeleton” with high cost and less than stellar ease of use, have adopted language such as “exosuit,” “wearable robotics,” and “wearable exo-muscles.” This article uses “exoskeleton” to refer to all types of wearable external support systems.
Many of the prototypes for exoskeletons use fabrics that feature air chambers (air muscles), artificial gel muscles and sensors, or “4D” materials that are bendable and twistable in some positions but can stiffen in others. These wearables fit tightly to the body, move with body motions, and are made out of soft, flexible materials.
POTENTIAL BENEFITS
Industries that require workers to perform lifting tasks have many instances of back injuries, shoulder injuries, and neck injuries. These injuries aren’t cheap, easily topping $100,000 in direct costs per incident if surgery is required. Many times, these injuries also reduce quality of life. Preventing them not only saves money: it helps keep workers healthy and avoid indirect “costs” such as physical pain that may never go away, family issues and stress, and lower income from shortened careers. Coworkers suffer too, due to the stress of being short-staffed; serious injuries can also lead to low morale among coworkers.
While many exoskeletons are still in prototype, they hold great promise for reducing injuries, and their potential applications in occupational health and safety have drawn attention from NIOSH. In a post to its Science Blog on March 4, NIOSH notes that lifting and handling materials and use of heavy tools contribute to musculoskeletal disorders (MSDs), which account for nearly 30 percent of workplace injuries and illnesses that result in time away from work. According to Liberty Mutual Insurance Company, in 2012 the costs of injuries from overexertion exceeded $15 billion.
NIOSH notes that the market for exoskeletons is expected to grow from $3 million in 2016 to more than $1 billion in 2021—not quite as large as the wearable technology market, but a tremendous increase nonetheless. The agency hasn’t yet conducted scientific studies on the potential benefits of exoskeletons for occupational safety and health. The blog post states that most existing studies of exoskeletons have been conducted in laboratories; calls for studies of long-term use in actual work environments; and identifies several issues that researchers might wish to address, such as the potential for transference of load between musculoskeletal regions that might put wearers at risk, the effects of exoskeletons on wearers’ sense of balance, and the potential for creating a “false sense of security” for wearers when handling heavy loads. NIOSH is also interested in determining how to safely adjust weight limits for lifting and handling of materials for workers wearing exoskeletons.
TYPES OF EXOSKELETONS
There are two categories of exoskeletons: active and passive. Active exoskeletons use a power source such as a battery or compressed air. Passive units either create a power source or have no need for one.
Applications of exoskeletons include tool handling, where the weight of a tool is supported; lift assistance, with the exoskeleton bearing a percentage of the load; position assistance, where a particular body position is supported; and physical therapy, in which the exoskeleton physically moves part of the body. The healthcare field is experiencing rapid growth in utilizing exoskeletons for both patient care as well as therapy, although the manufacturing and construction industries are gaining ground due to the length of time necessary for healthcare organizations to achieve approval from the Food and Drug Administration for use of these devices.
Passive Exoskeletons
Two kinds of passive exoskeletons are currently used in U.S. military settings. One unit absorbs shock and vibration to minimize stress on the knees while the wearer is standing and operating small watercraft. Personnel in the military, Coast Guard, police, and wildlife government agencies are using this unit while patrolling waterways. The other passive exoskeleton is worn on the torso like a backpack. It is designed specifically to manually lift and carry items such as boxes. According to the manufacturer, this device redistributes 50 to 70 percent of the weight of the load to other parts of the body (predominantly the legs and shoulders) while supporting the back in a proper lifting position.
Traditional passive exoskeletons—those with metal frames—are being used in heavy manufacturing for ship building and aerospace applications. These exoskeletons allow a worker to hold a tool weighing in excess of 40 pounds at arm’s length by reducing the muscle force requirement by 50 percent. The metal frame and springs transfer the load from the arm to the ground. Although these types of exoskeletons are being utilized and produced, they tend to be designed for a specific task and are therefore not generally marketed as mass-produced units.
Some passive exoskeleton prototypes are designed to create their own “power source.” These units have small air pumps or capacitors that harness energy from the pressure exerted on the wearer’s feet while walking. The energy captured in this manner can power the exoskeleton by activating a motor or filling an air chamber to actuate motion. This design has great potential for making an exoskeleton lighter and more cost effective.
Active Exoskeletons
If the movie “Ironman” comes to mind when you think of exoskeletons, you’re likely picturing an active exoskeleton (though as of yet, none can achieve flight). Active exoskeletons utilize a power source, usually a battery pack or a compressed air cylinder worn on the back. Many of these are zero-load devices: they support their own weight, and are therefore virtually weightless to the wearer. Some active exoskeletons are the bulky, steel-frame kind, which can lift several hundred pounds with no additional force from the wearer; generally, these are used only in R&D. Many other active exoskeletons are made of carbon fiber, plastics, aluminum, and even fabrics, giving them a sleeker, more attractive appearance, and less bulk for the wearer to maneuver.
Active exoskeletons have undergone years of research and development, mostly in the military and healthcare sectors. Most active exoskeletons are lift-assists (used by the military and in industrial and healthcare applications) or therapy units (healthcare). These types of exoskeletons tend to be complicated, with elaborate wiring harnesses, motors, relays, sensors, mini-computers, and hydraulics. Some are lower-body-only units for the hips and legs, while others are upper-body-only for the shoulders and arms (see Figure 1). There are also full-bodied exoskeletons.
Figure 1.
A worker wearing an upper-body-only exoskeleton. This device assists with lifting materials. Photo used with permission from StrongArm Technologies.Lower-body devices are being utilized in the patient rehabilitation field to help people learn or re-learn how to walk. The military also uses them to reduce fatigue on wearers (such as infantry personnel, for example) by supporting some of the weight of their gear and weapons and assisting with walking, allowing them to cover more ground. Some active exoskeletons utilize sensors that detect minute electrical impulses from the wearer’s nervous system; when the brain sends a signal for the leg to move, the exoskeleton moves in sync with the body. This isn’t future technology—these units are in production.
In healthcare, the highest injury costs are from back injuries workers incur while lifting patients. Hospitals, nursing homes, and other healthcare facilities are implementing team-lifting policies or using devices the size of a room to assist with lifting patients. These interventions leave a lot to be desired. Team lifts take time and require additional staff. In an emergency situation, when a patient has fallen, compassion takes precedence over self-preservation and workers react before getting help. Lifting devices are slow, cumbersome, and impersonal. A low-profile active exoskeleton could be the solution to these problems. One full-body active exoskeleton, according to its manufacturer, allows the wearer to lift a patient weighing nearly 200 pounds without any additional strain beyond simply standing up.
THE FUTURE
Several R&D companies, as well as numerous college ergonomics and robotics departments, are working on further development of exoskeletons. Designs in the works include those for use in hazardous environments and rescue operations. The A.F.A. (advanced firefighting apparatus) is a powered exoskeleton designed to aid fire fighters; it would support its own weight plus the additional weight of gear (125 pounds for most firefighters) and allow wearers to carry a victim as well as tools such as an on-board “jaws-of-life” mechanism. It also features a pressurized water cannon attached to the forearm.
Another design idea is an environmental exosuit for disaster recovery and radiation emergencies. This exoskeleton would protect the wearer from highly toxic atmospheres such as radiation leaks and could potentially be used in conditions appropriate for a Level A Hazmat suit, though the exoskeleton would be less bulky, include air conditioning and a drinking fountain, support the weight of an air tank, and reduce fatigue for the wearer. Designs for military and law enforcement applications are utilizing lightweight body armor that could prevent shrapnel or direct fire from piercing the exosuit and absorb impact before reaching the wearer’s body.
In the next five years, exoskeleton prototypes will become production units, and new prototypes will advance opportunities for additional exoskeleton variations. The use of soft fabrics, air/gel muscles, motors, sensors, and self-powering options will improve the functionality and efficiency of exoskeletons while reducing costs, leading to additional applications in industry, healthcare, the military, and possibly even in the home. While research is needed to assess exoskeletons’ long-term effects on wearers’ health and safety, it’s likely that some industrial hygienists will soon see exoskeletons in their workplaces. The potential for reducing stressors on the body and preventing injuries will drive the production of exoskeletons from novel technological wonders to common ergonomic aids.
MICK SNYDER, CIH, CSP,
is the EHS Specialist at LSI Solutions, Inc. in Victor, N.Y. He has served as president of AIHA’s Western New York Local Section and is a member of the AIHA Computer Applications Committee. He can be reached at (585) 739-8768 or msnyder@lsisolutions.com
.RESOURCES
This article draws from information available on the websites of exoskeleton manufacturers, including 20KTS+, Cyberdyne, Ekso Bionics, Indego, Sarcos, Lockheed Martin, ReWalk, REX Bionics, SuitX, and StrongArm Technologies. Other sources include:
Cynergy Ergonomics: “
Comparing the Direct vs. Indirect Costs of Work-Related Injuries
” (April 2014).
DamnGeeky: “
Designer Builds Exoskeleton Suit for Firefighters
” (2015).
Exoskeleton Report: “
Exoskeletons Extracting Energy from the User
” (May 2015).
Exoskeleton Report: “
Unplugged Powered Suit—Associate Professor Yuichi Kurita
” (December 2015).
Mashable: “
Panasonic Gives Us Our First Look at Bionic Factory Workers
” (March 2016).
Medical News Today: “
Healthcare Most Dangerous Place for Workplace Injuries
” (July 2013).
NIOSH Science Blog: “
Wearable Exoskeletons to Reduce Physical Load at Work
” (March 2016).
Statista: “
Facts and Statistics on Wearable Technology
” (2016).thesynergist | TOC | NEWSWATCH | DEPARTMENTS | COMMUNITY